Wire Drawing and Flattening Machine Basics
Key Components and Functionality of Wire Drawing Machines
Essential Parts: Dies, Rollers, and Tension Systems
The essential components of a wire drawing machine play a critical role in determining the quality and efficiency of the wire being produced. The die is arguably the most crucial element, as it determines the final diameter and surface quality of the wire. With precision engineering, dies ensure the wire maintains uniformity throughout the drawing process. Rollers are equally important, offering guidance and reducing friction as the wire passes through the machine, which also helps to minimize wear on both the wire and the machine. Additionally, tension systems are integral, maintaining the appropriate force to prevent wire breakage and ensure uniform drawing. This combination of components ensures the machine can produce high-quality wire consistently.
How Wire Flattening Complements Drawing Processes
Integrating wire flattening into the drawing process offers significant enhancements for various industrial applications. The primary benefit of wire flattening is an increase in the surface area of wires, which is particularly valuable in the electrical industry for better conductivity. By reducing the steps involved in the wire production process, combining drawing and flattening can streamline operations, leading to higher efficiency and less downtime. This is especially vital for industries like automotive and electronics, where specialized wire profiles are required. This integration also allows for the creation of wires with specific dimensions and shapes tailored to precise application needs.
The Role of Wire Preparation in Efficient Operation
Proper wire preparation is a crucial step in ensuring efficient operation and high-quality output from a wire drawing machine. This preparatory phase often involves cleaning and annealing the wire, which reduces defects and ensures smoother drawing results. Adequate preparation also minimizes the likelihood of irregularities, helping maintain consistency throughout production. Regular checks and maintenance of the preparation process are also important to ensure that the machine operates efficiently and that the final product meets desired quality standards. This focus on preparation helps maximize the machine’s performance, offering both operational efficiency and superior product output.
Types of Wire Drawing Machines Explained
Straight Line Carbon Wire Drawing Machines
Straight line carbon wire drawing machines are designed with a straightforward layout that significantly enhances the efficiency of carbon wire processes. This simple yet effective design minimizes unnecessary movement within the machine, thereby reducing wear and tear on its components. As a result, these machines are notably robust and less prone to mechanical failure, making them a popular choice in industrial applications where reliability and simplicity are paramount. The straight-line configuration ensures uniform wire tension and reduces the frequency of component replacements, contributing to lower operational costs. You can learn more about these machines by exploring the [Straight Line Carbon Wire Drawing Machine].
Pulley-Type vs. Water Tank Machines
Pulley-type wire drawing machines capitalize on a system of pulleys to improve the speed and efficiency of the wire drawing process. This system optimizes the tension and feed rate of the wire, resulting in high production throughput. Conversely, water tank machines are specially designed to manage the heat and lubrication challenges that arise during the drawing process. By controlling temperature and providing adequate lubrication, they extend the lifespan of the dies and rollers significantly. Understanding the operational differences between these two types of machines is crucial for manufacturers to select the machinery best suited to their specific needs and production goals. For more details, visit the [Pulley-Type Wire Drawing Machine].
Specialized Extremely Fine Wire Systems
Specialized extremely fine wire systems are engineered to produce wires with diameters as small as a few micrometers. This requires precision engineering and advanced technology to handle the delicate nature of the wire drawing process. Such systems include innovations that prevent wire breakage and ensure consistent quality across the production cycle. They are particularly useful in high-precision fields such as telecommunications, medical devices, and aerospace parts, where the accuracy of the wire dimensions is critical. The role of these machines in facilitating complex applications cannot be overstated, with part designs dependent on dependable and accurate wire production. Delve deeper into these systems by visiting [Extremely Fine Wire Drawing Machine].
Critical Features for Optimal Performance
High-Strength Alloy Construction
Using high-strength alloys in constructing wire drawing machines significantly boosts their durability and resistance to wear. These materials are designed to endure the intense stress and continuous operation typical in industrial settings, thereby prolonging the machine's lifespan. By minimizing breakdowns and maintenance needs, manufacturers can reduce downtime, which ultimately translates into lower operational costs and higher productivity.
Precision Control Systems
Modern wire drawing machines incorporate advanced precision control systems to ensure consistent product quality. These systems enable real-time adjustments to variables like speed and tension, which help minimize defects during the drawing process. Automation, integrated with precision control, further enhances production efficiency by maintaining optimal settings throughout operations, ensuring uniformity in the wire's specifications.
Automation in Modern Wire Processing
Automation in wire processing revolutionizes the way wire drawing procedures are carried out, from drawing to flattening, by reducing reliance on manual labor. Advanced software takes over machine operations, providing improved accuracy and minimizing the scope for human error. Additionally, automated systems facilitate the collection of operational data, offering insights that drive continuous improvement and better decision-making in manufacturing environments.
Industry Applications and Use Cases
Electrical Wiring Production
Wire drawing machines are essential in the production of electrical wiring, widely used in both residential and commercial settings. During the wire drawing process, specific wire properties such as conductivity and flexibility are carefully achieved. These properties are crucial for electrical applications as they ensure the safe and efficient transmission of electricity. The process must adhere to stringent industry standards to mitigate risks and enhance performance. By maintaining consistent quality, wire drawing machines help in producing high-quality electrical wires that meet these essential operational standards.
Nail Manufacturing Processes
In nail manufacturing, the wire drawing process is critical for producing nails with the appropriate thickness needed for strength and functionality. By ensuring precise control over wire dimensions, manufacturers can minimize defects and improve the durability of their products. This capability is particularly important as it enables manufacturers to achieve faster production cycles without sacrificing quality. Efficient wire drawing machines, often equipped with advanced control systems, reduce waste and enhance production efficiency, making them invaluable in the nail industry.
Aerospace Component Fabrication
In the aerospace industry, wire drawing machines are integral to producing high-strength wires that meet rigorous safety standards. These wires are often necessary for critical parts where reliability is paramount. The wire drawing process in aerospace involves specialized techniques that enhance wire properties, ensuring they can withstand the unique stresses encountered in flight conditions. By collaborating closely with aerospace manufacturers, wire drawing facilities can ensure that their products meet the stringent technical specifications required for these demanding applications. This collaboration guarantees that safety and performance are never compromised in aerospace component fabrication.
Maintenance and Operational Best Practices
Lubrication and Wear Prevention
Regular lubrication of moving parts is crucial in preventing wear and extending the lifespan of wire drawing machines. The use of appropriate lubricants ensures that the machine operates smoothly by reducing friction and preventing overheating during prolonged use. Systematic scheduled maintenance checks help identify signs of wear early, allowing for timely interventions that prevent costly breakdowns. This approach not only preserves the optimal functioning of machines but also supports continuous production, integral to maintaining competitiveness in high-demand environments like wire reel winder machine operations and factories.
Troubleshooting Common Tension Issues
Early identification of tension issues in wire drawing machines can significantly save time and maintain the quality of produced wire. Misalignment of the wire path and incorrect settings are frequent causes of tension problems. By conducting regular checks and recalibrating settings, these issues can be minimized. Moreover, a systematic troubleshooting guide proves invaluable for operators, as it equips them to quickly resolve tension-related challenges, ensuring machines like the straight line carbon wire drawing machine maintain peak performance.
Extending Machine Lifespan
Adopting a preventive maintenance schedule is essential for significantly extending the lifespan of wire drawing machines. Operators should be well-trained in best practices, focusing on regular adjustments and routine checks to prevent unnecessary wear. Additionally, investing in high-quality parts for repairs and replacements is wise as it ensures optimal performance over time. This practice not only guarantees the machine's longevity but also its efficiency, a critical requirement in industries where machines, such as the extremely fine wire drawing machine, are indispensable.
KY Pneumatic Wire Drawing and Flattening Machine
Technical Specifications: 380V Motor & 350-600m/min Speed
The KY Pneumatic Wire Drawing and Flattening Machine boasts a robust 380V motor, providing the necessary power for demanding industrial applications. This high-performance motor supports speeds ranging from 350 to 600 meters per minute, making it ideal for environments focused on high-volume production. Such capabilities ensure that manufacturers can meet rigorous output requirements while maintaining efficiency and reliability.
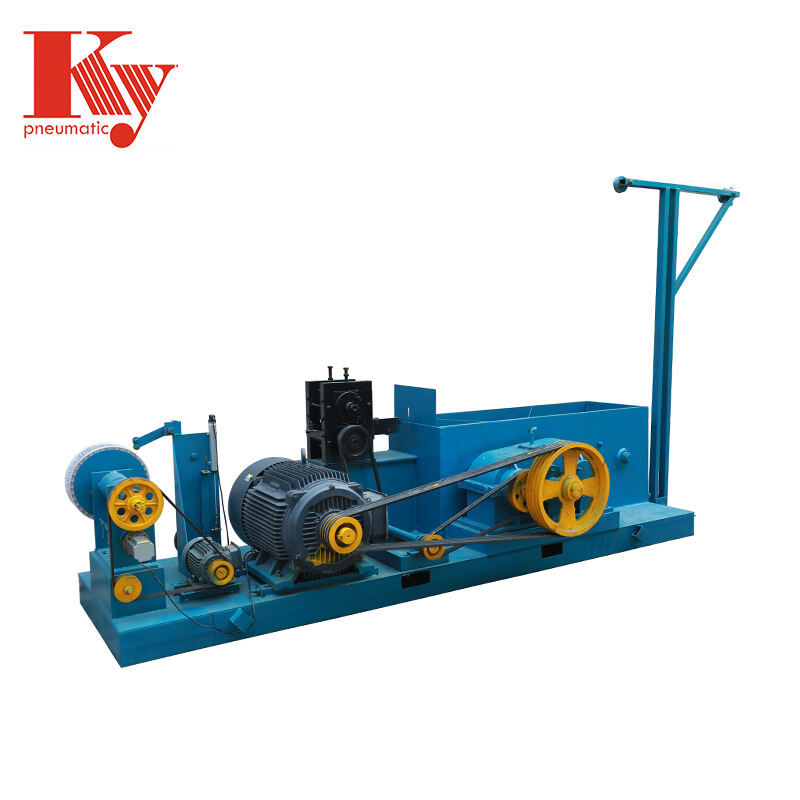
High-Precision Flattening Capabilities
This machine incorporates cutting-edge technology that ensures ultra-precise wire flattening, meeting the stringent specifications required in various industrial applications. Enhanced precision not only improves product quality but also minimizes material wastage, contributing to more cost-effective operations. By maintaining consistency and accuracy, it supports manufacturers most demanding flattening projects.
Ideal for Diverse Wire Diameters (0.5-2.0mm)
The KY machine's versatility extends to handling various wire diameters, ranging from 0.5 to 2.0mm. This adaptability is crucial for manufacturers aiming to diversify their product lines and accommodate different market needs. By efficiently processing a wide range of diameters, this machine stands as an invaluable asset for businesses looking to expand capabilities and enhance competitiveness in wire manufacturing.