Podstawy maszyny do wyciągania i spłaszczania drutu
Podstawowe Komponenty i Funkcjonalność Maszyn do Wyciągania Drutu
Podstawowe Części: Matryce, Rolki i Systemy Napięcia
Podstawowe elementy maszyny do wyciągania drutu odgrywają kluczową rolę w określeniu jakości i wydajności produkowanego drutu. Matryca jest zapewne najważniejszym elementem, ponieważ decyduje o końcowym średnicy i jakości powierzchni drutu. Dzięki precyzyjnej inżynierii matryce zapewniają, że drut zachowuje jednostajność przez cały proces wyciągania. Rolki są równie ważne, oferując kierowanie i redukując tarcie podczas przechodzenia drutu przez maszynę, co również pomaga zmniejszyć zużycie zarówno drutu, jak i maszyny. Ponadto systemy napięcia są integralnym elementem, utrzymując odpowiednią siłę, aby zapobiec łamaniu drutu i zapewnić jednostajne wyciąganie. Ta kombinacja elementów gwarantuje, że maszyna może produkować wysokiej jakości drut zgodnie.
Jak spłaszczanie drutu uzupełnia procesy wyciągania
Integrowanie wypłaszczania przewodów do procesu wydłużania oferuje istotne ulepszenia dla różnych zastosowań przemysłowych. Główną zaletą wypłaszczania przewodów jest zwiększenie ich powierzchni, co jest szczególnie cenne w przemyśle elektrycznym ze względu na lepszą przewodność. Poprzez zmniejszenie liczby kroków w procesie produkcji przewodów, łączenie wydłużania i wypłaszczania może zoptymalizować działania, prowadząc do większej efektywności i mniej czasu simplyfikacji. Jest to szczególnie ważne dla branż, takich jak motoryzacyjna i elektroniczna, gdzie wymagane są specjalne profile przewodów. Ta integracja umożliwia również produkcję przewodów o określonych wymiarach i kształtach dopasowanych do konkretnych potrzeb aplikacyjnych.
Rola przygotowania przewodów w efektywnym działaniu
Poprawne przygotowanie przewodu jest kluczowym krokiem w zapewnieniu wydajnego działania i wysokiej jakości wyjściowej z maszyny do wyciągania przewodów. Ta faza przygotowawcza często obejmuje czyszczenie i wykałaczanie przewodu, co redukuje defekty i gwarantuje płynniejsze wyniki wyciągania. Wystarczające przygotowanie minimalizuje również prawdopodobieństwo niezgodności, pomagając utrzymać spójność przez cały proces produkcyjny. Regularne kontrole i konserwacja procesu przygotowawczego są również ważne, aby upewnić się, że maszyna działa efektywnie, a ostateczny produkt spełnia wymagane standardy jakości. Ten nacisk na przygotowanie pomaga maksymalizować wydajność maszyny, oferując zarówno efektywność operacyjną, jak i wyższą jakość wyjścia produktu.
Rodzaje maszyn do wyciągania przewodów wytłumaczone
Maszyny do wyciągania przewodów węglowych typu linia prosta
Maszyny do wyciągania drutu węglowego o układzie liniowym zostały zaprojektowane z prostą konstrukcją, która znacząco zwiększa wydajność procesów drutu węglowego. Ten prosty, lecz skuteczny projekt minimalizuje niepotrzebne ruchy wewnątrz maszyny, co redukuje zużycie jej elementów. W rezultacie te maszyny są wyjątkowo trwałe i mniej podatne na awarie mechaniczne, co czyni je popularnym wyborem w zastosowaniach przemysłowych, gdzie kluczowe są niezawodność i prostota. Konfiguracja liniowa zapewnia jednolite napięcie drutu i zmniejsza częstotliwość wymiany elementów, co przekłada się na niższe koszty eksploatacji. Więcej na temat tych maszyn możesz dowiedzieć się, badając [Straight Line Carbon Wire Drawing Machine].
Maszyny typu koło uzębione vs. z basenem wodnym
Maszyny do wyciągania drutu typu kołowrotowego wykorzystują system kołek, aby zwiększyć prędkość i wydajność procesu wyciągania drutu. Ten system optymalizuje napięcie i szybkość zasilania drutu, co prowadzi do wysokiej przepustowości produkcji. Natomiast maszyny z zbiornikiem wodnym są specjalnie zaprojektowane do zarządzania problemami związanymi z temperaturą i smarowaniem podczas procesu wyciągania. Kontrolując temperaturę i zapewniając odpowiednie smarowanie, znacznie przedłużają żywotność matryc i wałków. Zrozumienie różnic operacyjnych między tymi dwoma rodzajami maszyn jest kluczowe dla producentów przy wybieraniu urządzeń najlepiej dopasowanych do ich konkretnych potrzeb i celów produkcyjnych. Aby uzyskać więcej szczegółów, odwiedź [Maszynę do Wyciągania Drutu Typu Kołowrotowego].
Specjalistyczne Systemy dla Ekstremalnie Cienkich Drutów
Specjalistyczne systemy ekstremalnie cienkich drutów są zaprojektowane do produkcji drutów o średnicach tak małych, że mogą wynosić zaledwie kilka mikrometrów. Wymaga to precyzyjnej inżynierii i zaawansowanej technologii do obsługi delikatnej natury procesu wyciągania drutów. Takie systemy obejmują innowacje, które zapobiegają łamaniu drutów i gwarantują stały poziom jakości przez cały cykl produkcji. Są one szczególnie przydatne w dziedzinach wymagających wysokiej precyzji, takich jak telekomunikacja, urządzenia medyczne i części lotnicze, gdzie dokładność wymiarów drutów jest krytyczna. Rolę tych maszyn w umożliwieniu złożonych zastosowań nie można przeszacować, ponieważ projekty elementów zależą od niezawodnej i dokładnej produkcji drutów. Dowiedz się więcej na ten temat, odwiedzając [Maszynę do Wyciągania Ekstremalnie Cienkich Drutów].
Kluczowe funkcje dla optymalnego wydajności
Konstrukcja z wysokoprężnych stopów
Użycie wysokoprzyczynowych stopów w konstrukcji maszyn do ciągnięcia drutów znacząco zwiększa ich trwałość i oporność na zużycie. Te materiały są projektowane tak, aby wytrzymać intensywny stres i ciągłe działanie charakterystyczne dla warunków przemysłowych, co przedłuża żywotność maszyny. Minimalizując awarie i potrzeby konserwacji, producenci mogą zmniejszyć czas nieczynności, co ostatecznie przekłada się na niższe koszty eksploatacji i większą produkcyjność.
Systemy precyzyjnej kontroli
Nowoczesne maszyny do ciągnięcia drutów integrują zaawansowane systemy sterowania precyzją, aby zapewnić spójną jakość produktu. Te systemy umożliwiają korekty w czasie rzeczywistym zmiennych takich jak prędkość i napięcie, co pomaga zminimalizować defekty podczas procesu ciągnięcia. Automatyzacja, zintegrowana z kontrolą precyzji, dalej poprawia efektywność produkcji, utrzymując optymalne ustawienia w trakcie operacji, co gwarantuje jednolitość specyfikacji drutu.
Automatyzacja w nowoczesnym przetwarzaniu drutów
Automatyzacja w przetwarzaniu przewodów rewolucjonizuje sposób wykonywania procedur ciągnienia przewodów, od ciągnięcia do spłaszczenia, poprzez zmniejszenie zależności od ręki roboczej. Zaawansowane oprogramowanie przejmuje operacje maszynowe, zapewniając lepszą dokładność i minimalizując ryzyko błędu ludzkiego. Ponadto, systemy automatyczne ułatwiają zbieranie danych operacyjnych, oferując wgląd, który prowadzi do ciągłej poprawy i lepszego podejmowania decyzji w środowiskach produkcyjnych.
Zastosowania w przemyśle i przykłady użycia
Produkcja instalacji elektrycznych
Maszyny do wyciągania drutu są niezbędne w produkcji instalacji elektrycznych, szeroko stosowanych zarówno w budynkach mieszkalnych, jak i komercyjnych. W trakcie procesu wyciągania drutu określone właściwości drutu, takie jak przewodnictwo i giętkość, są starannie osiągane. Te właściwości są kluczowe dla zastosowań elektrycznych, ponieważ zapewniają bezpieczną i wydajną transmisję prądu. Proces musi przestrzegać surowych standardów branżowych, aby zmniejszyć ryzyka i poprawić wydajność. Dzięki utrzymywaniu spójnej jakości maszyny do wyciągania drutu pozwalają na produkcję wysokiej jakości przewodów elektrycznych, które spełniają te podstawowe standardy operacyjne.
Procesy produkcyjne gwoździ
W produkcji gwoździ, proces wyciągania drutu jest kluczowy dla wyprodukowania gwoździ o odpowiedniej grubości potrzebnej do ich wytrzymałości i funkcjonalności. Dzięki precyzyjnemu sterowaniu wymiarami drutu, producenci mogą minimalizować defekty i poprawiać trwałość swoich produktów. Ta umiejętność jest szczególnie ważna, ponieważ pozwala producentom osiągnąć szybsze cykle produkcji bez rezygnacji z jakości. Wydajne maszyny do wyciągania drutu, często wyposażone w zaawansowane systemy sterowania, redukują marnotrawstwo i zwiększają efektywność produkcji, czyniąc je nieocenionymi w przemyśle gwoździanym.
Produkcja elementów lotniczych
W przemyśle lotniczym maszyny do wyciągania drutów są kluczowe przy produkcji drutów o wysokiej wytrzymałości, które spełniają surowe normy bezpieczeństwa. Te druty są często niezbędne w elementach krytycznych, gdzie niezawodność ma podstawowe znaczenie. Proces wyciągania drutów w przemyśle lotniczym obejmuje specjalistyczne techniki, które poprawiają właściwości drutów, zapewniając, że mogą wytrzymać unikalne naprężenia występujące w warunkach lotu. Współpraca z producentami lotniczymi pozwala zakładom wytwarzającym druty na zapewnienie, że ich produkty spełniają ścisłe wymagania techniczne związane z tymi wymagającymi zastosowaniami. Ta współpraca gwarantuje, że bezpieczeństwo i wydajność nigdy nie są kompromitowane podczas produkcji elementów lotniczych.
Konserwacja i najlepsze praktyki operacyjne
Lubrynacja i zapobieganie zużyciu
Regularyczne smarowanie części ruchomych jest kluczowe w zapobieganiu zużyciu i przedłużaniu żywotności maszyn do wyciągania drutów. Używanie odpowiednich smarów gwarantuje, że maszyna działa płynnie, redukując tarcie i zapobiegając przegrzaniu podczas długotrwałego użytkowania. Systematyczne planowane kontrole konserwacyjne pomagają zidentyfikować znaki zużycia na wczesnym etapie, pozwalając na timely interwencje, które zapobiegają drogim awariom. Ten sposób nie tylko zachowuje optymalne działanie maszyn, ale również wspiera ciągłą produkcję, która jest istotna dla utrzymania konkurencyjności w środowiskach o wysokim popycie, takich jak operacje maszyn do wycinania bobin drutów i fabryki.
Rozwiązywanie typowych problemów z napięciem
Wczesne identyfikowanie problemów z napięciem w maszynach do ciągnięcia drutu może znacząco oszczędzić czas i utrzymać jakość produkowanego drutu. Niewłaściwe wyrównanie ścieżki drutu i niepoprawne ustawienia są częstymi przyczynami problemów z napięciem. Przeprowadzanie regularnych kontroli i ponowne kalibrowanie ustawień pozwala minimalizować te problemy. Ponadto systematyczny przewodnik rozwiązywania problemów okazuje się nieoceniony dla operatorów, ponieważ wyposaja ich umiejętnością szybkiego rozwiązywania wyzwań związanych z napięciem, co zapewnia, że maszyny, takie jak maszyna do ciągnięcia drutu węglowego o linii prostej, utrzymują maksymalną wydajność.
Przedłużanie żywota maszyny
Wprowadzenie harmonogramu konserwacji przewencyjnej jest kluczowe dla istotnego przedłużenia żywotności maszyn do wyciągania drutów. Operatorzy powinni być dobrze wykształcczeni w najlepszych praktykach, skupiając się na regularnych dostosowaniach i rutynowych kontrolach, aby zapobiec niepotrzebnemu zużyciu. Ponadto, inwestycja w wysokiej jakości części do napraw i zamienników jest mądrym krokiem, ponieważ zapewnia optymalne wydajność w czasie. Ta praktyka gwarantuje nie tylko dłuższy żywot maszyny, ale również jej efektywność, co jest kluczowym wymaganiem w branżach, gdzie maszyny, takie jak ekstremalnie cienkie maszyny do wyciągania drutów, są niezastąpione.
KY Pneumatic Wire Drawing and Flattening Machine
Specyfikacje techniczne: Motor 380V & Prędkość 350-600m/min
Maszyna KY Pneumatyczna do wyciągania i spłaszczania drutów dysponuje mocnym silnikiem 380V, zapewniającym niezbędną moc dla wymagających zastosowań przemysłowych. Ten wysokowydajny silnik obsługuje prędkości od 350 do 600 metrów na minutę, co czyni go idealnym dla środowisk skupionych na produkcji w dużych objętościach. Takie możliwości gwarantują, że producenci mogą spełnić surowe wymagania dotyczące wydajności, zachowując efektywność i niezawodność.
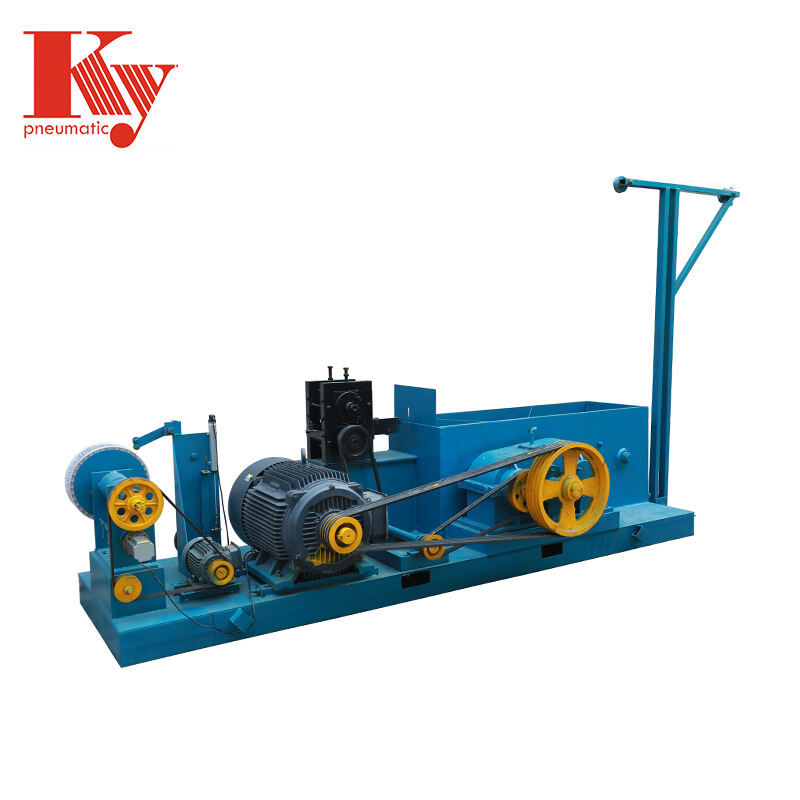
Wysokoprecyzyjne możliwości spłaszczania
Ten aparat integruje nowoczesną technologię, która zapewnia ultra-precyzyjne wypłaszczanie drutu, spełniając surowe wymagania potrzebne w różnych zastosowaniach przemysłowych. Zwiększona precyzja nie tylko poprawia jakość produktu, ale również minimalizuje marnotrawstwo materiału, co przyczynia się do bardziej opłacalnych operacji. Dzięki utrzymywaniu spójności i dokładności, wspiera producentów w ich najbardziej wymagających projektach wypłaszczania.
Idealny dla różnorodnych średnic drutu (0,5-2,0mm)
Wielofunkcyjność maszyny KY rozszerza się na obsługę różnych średnic drutu, od 0,5 do 2,0mm. Ta elastyczność jest kluczowa dla producentów dążących do zróżnicowania swoich linii produktów i dostosowania się do różnych potrzeb rynkowych. Efektywna obróbka szerokiego zakresu średnic czyni z tej maszyny cenny atut dla firm chcących rozwijać możliwości i zwiększać konkurencyjność w produkcji drutu.